Polysulfone is a member of the sulfone polymer group, a class of engineering thermoplastics with excellent mechanical and thermal properties and the ability to resist degradation from exposure to steam and many chemicals. Specific versions of sulfone polymers are polysulfone (PSU), polyphenylsulfone (PPSU) and polyethersulfone (PES). In the medical device industry, polysulfone and PPSU are the most common types of these thermoplastics.
These polymers are termed sulfones because they have polymeric structures built on SO2 or sulfur dioxide groups linked to a chain of aromatic rings. All are amorphous thermoplastics and share many common characteristics associated with these types of materials, including transparency, dimensional stability, and melt processability by injection molding and extrusion.
Polysulfone and PPSU Properties
Both polysulfone (PSU) and PPSU are high performance medical grade plastics that exhibit the following characteristics:
- Excellent resistance to hydrolysis – Polysulfone and PPSU polymers remain stable when exposed to high temperature water and steam, making them viable candidates for medical instruments that must undergo repeated autoclaving. PSU performs well after 100 cycles at standard autoclave temperatures of 134o C or 274o PPSU maintains a high level of its original physical properties such as rigidity and ductility even up to 1000 autoclave cycles at these temperatures.
- Comprehensive biocompatibility – PSU and PPSU grades have been developed for medical devices that require long-term biocompatibility. Eviva PSU and Veriva® PPSU, both developed by Syensqo (formerly Solvay Specialty Polymers), meet regulatory requirements for use as long-term implantable materials for devices in contact with bodily tissue and fluids for 30 days or more. Both are manufactured according to ISO 13485 and cGMP guidelines, and tested in ISO 9001 and ISO 17025-approved laboratories.
In addition, standard grades of polysulfone and PPSU are used in medical devices that are in contact with bodily fluids and tissue short-term, or less than 24 hours. - Excellent high temperature performance – Sulfone polymers rank at the high end of thermal performance, along with some semicrystalline materials such as PEEK. Based on ASTM testing, polysulfone has a heat deflection temperature (HDT) of 345o F or 174o PPSU’s HDT measures even higher, at 405o F or 207o C. Their thermal resistance means PSU and PPSU are suitable for applications in hot sterilization processes and in components and housings for heat-generating equipment used in laboratories.
- Combination of flexibility, strength and toughness – Both polysulfone and PPSU offer rigidity based on their high tensile and flexural strength. They are also tough, with high impact resistance. The materials also are dimensionally stable in aqueous and steam environments and under physical load. They resist creep or deformation under load over time, but PPSU performs somewhat better in this area.
- Broad chemical resistance – Sulfone polymers are inherently resistant to attack from many types of chemicals associated with health care environments, including strong bases and acids.
- Electrical insulation and flame resistant properties – PPSU and polysulfone have dielectric properties that make them effective for applications requiring electrical insulation. They are also rated 94V-0 on flammability. These combined attributes have led to their use as materials for housings and components in electrical monitoring and analytical equipment and similar devices requiring UL approval. PPSU is also often specified as a material for coating wires and electrical leads.
Medical Applications for Polysulfone and PPSU Polymers
Sulfones are extensively utilized in many medical devices given their biocompatibility, resistance to deterioration from repeated sterilization, and their mechanical strength and toughness. Polysulfone’s very light natural tint is a particular benefit for applications requiring transparency. PPSU has a darker amber natural tint, and is available in standard healthcare colors that are highly stable when exposed to repeated sterilization cycles.
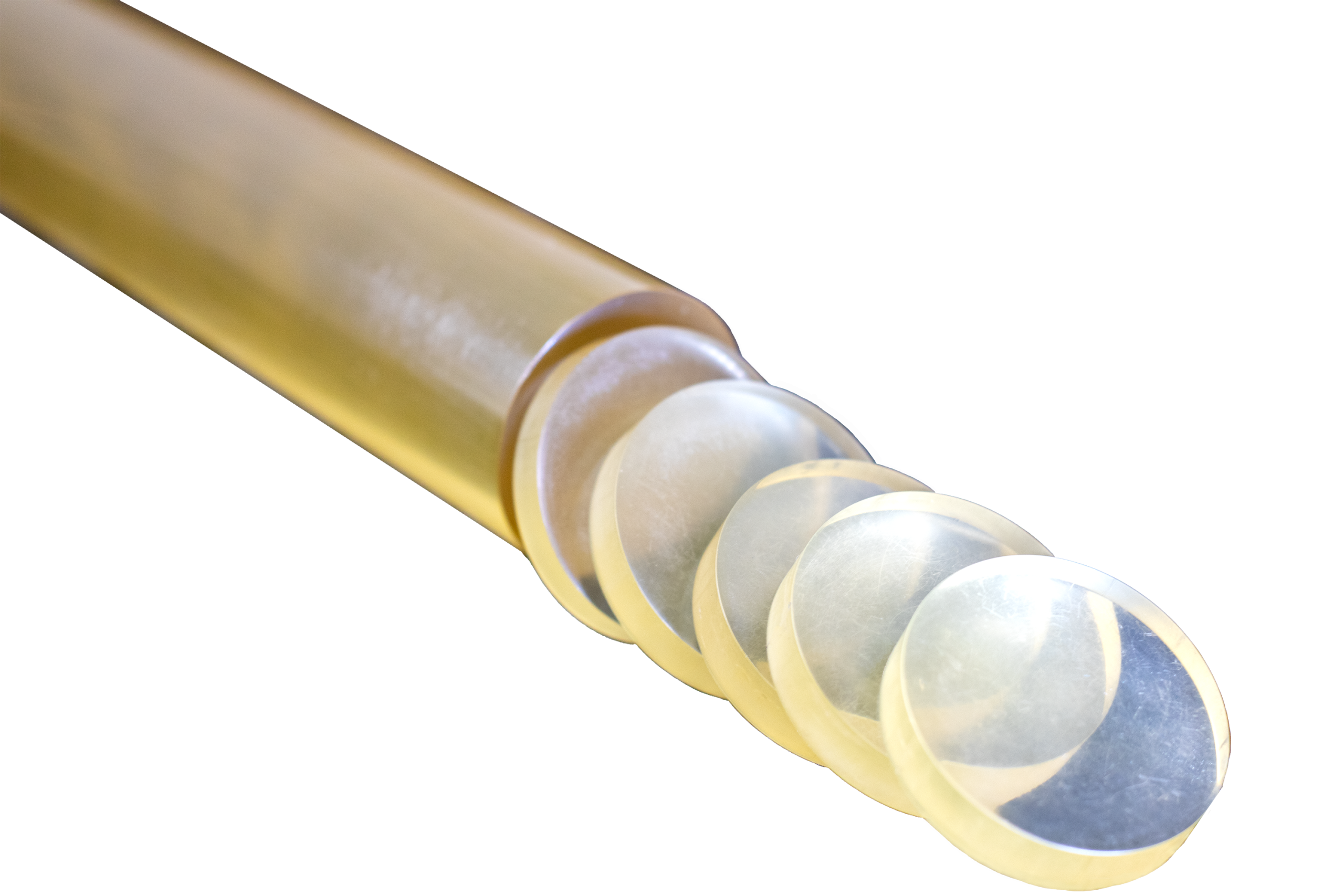
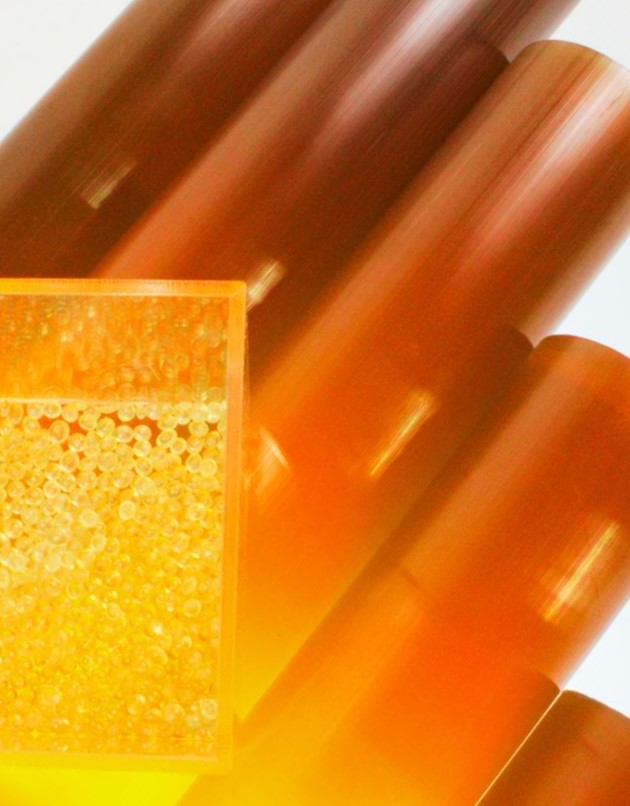
Specialized versions of PSU and PPSU polymers are also among the few medical plastics along with PEEK that can be used for long-term implantable medical devices in contact with bodily tissue and fluid for 30 days or longer.
Common medical applications for polysulfone and PPSU include:
- Medical equipment housings
- Dialysis equipment components including filtration devices
- Filtration membranes
- Sterilization containers and trays
- Heart valve sizing trials, heart valves and shunts
- Blood oxygenators
- Medical fittings and connectors
- Surgical devices such as retractors, clamps, forceps and joint sizing trials
- Surgical instrument handles
How a Medical Polymers Specialist Can Optimize PSU and PPSU Performance
Taking a medical device from design to launch is a long, complex journey. Unknowns related to materials can lead to delays and budget overruns. Some of these potential delays are often associated with material selection and design and material validation through testing.
Capable medical polymer converters have the experience required in material properties. They also offer prototyping as well as injection molding, shapes extrusion and machining to facilitate progress from medical device development through production. Consider the benefits a specialized medical grade plastics processor can provide:
- Support in defining the right balance of material performance and cost
Medical grade plastics processors can help define and minimize the number of candidate polymers and specific grades that MDMs should evaluate. An experienced company will have strong working ties to medical polymer resin suppliers for detailed performance data as well as access to their technical support teams as needed.
- Fast turn-around times on prototypes in candidate materials
A medical plastics converter with the right facilities can work with the MDM’s product team on developing prototype parts to validate the device’s design and performance in the range materials chosen for testing. This can require many design iterations in the early stages, making turn-around times an asset.
The ability to extrude semi-finished shapes for machining in the candidate materials is a major asset, coupled with CNC machining equipment to produce the prototype parts quickly. This combination can also help later in the development process, when alpha, beta, and pilot prototypes in the specified material are necessary for regulatory submittals and for lab or clinical trials.
- Injection molding tool design, construction and fine-tuning
Experience in designing, building and adapting tooling quickly when required is also an important factor for choosing a capable medical plastics converter. As projects move from machined or molded prototypes and approach high volume production in injection molding, tooling expertise and tool modification capabilities are keys to minimizing delays. These skills are particularly important once in full-scale injection molding production, should slight modifications be required to maintain product introduction deadlines or as a product’s design evolves through its life-cycle.
- Material characterization and melt-processing expertise
A medical plastics processor with robust melt characterization equipment can define the injection molding or extrusion process conditions that will deliver the highest levels of performance from the specified material. Additionally, an investment in state-of-the-art process controls will ensure that the optimum conditions of pressure and temperature are maintained and can be adjusted instantaneously if needed.
- Access to support information from concept to regulatory approval
Medical plastics specialists can provide access to material data, lab testing results, and biocompatibility reports which can facilitate the many stages of device development and approval, from early design and functional concepts to regulatory agency submittals.
Combining Polysulfone and PPSU Performance with Processing Expertise for High Quality and Reliability
Polysulfone and PPSU offer a proven combination of physical properties, sterilization resistance, biocompatibility and cost-effectiveness for long-term dependability. When converted into prototypes and finished parts by a specialist skilled in processing these materials, MDMs have the combination of factors that delivers the quality and performance they expect for their devices.