Polysulfone (PSU) and polyphenylsulfone (PPSU) are both members of the sulfone family of amorphous polymers. They are considered high performance plastics and are widely specified for a variety of medical device applications. While they possess similar mechanical properties and chemical resistance, PPSU, available commercially as Radel, has a notably longer sterilization life after multiple cycles.
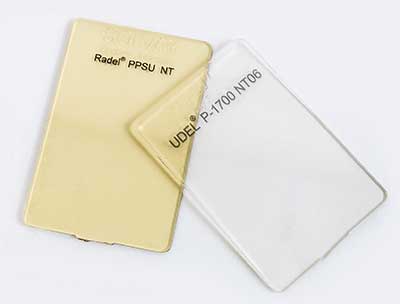
The two polymers are available in opaque colors that serve numerous health care applications, as well as in transparent tints for devices where monitoring of fluids is necessary. Polysulfone has a significantly lighter tint than PPSU, a factor behind its use where maximum visibility is essential.
Both PSU and PPSU demonstrate excellent biocompatibility. The standard grades can be used for medical devices with short-term exposure to bodily fluids (up to 24 hours), while specialized versions of each material have been developed for use in long-term and permanently implantable applications.
The following summary compares PSU and PPSU on performance and describes some of the typical medical applications for each of the polymers:
A Comparison of PSU and PPSU Properties Important in Medical Devices
Polysulfone and Radel PPSU are both used extensively in medical devices. They fill slightly different roles based on the differences in how they perform. Here’s how the performance attributes of the polymers compare:
- Flexural modulus – PSU has a slight advantage over PPSU in terms of modulus or rigidity. Relative to other polymers used in the medical industry, both compare favorably to polycarbonate (PC) and polyoxymethylene (POM-C). Their stiffness is a particular asset for hand-held instruments where flexing would be problematic.
- Impact resistance and resilience – PSU and PPSU both provide excellent impact strength, a benefit for the durability of devices. Their tensile strength is also comparable, but PPSU is a more ductile material and exhibits a higher tensile elongation.
- Chemical resistance – PSU and PPSU exhibit good resistance to a wide range of chemicals including most disinfectants and cleaners used in medical environments, Both withstand strong acids and bases, but PPSU is much more resistant to solvents.
- Sterilization resistance – PSU and PPSU can withstand hundreds of steam sterilization cycles, depending on the temperature of the system. Specifically, PSU performs well in lower-temperature autoclaving at 250oF or 121oC, while PPSU can tolerate steam sterilization at 273oF or 134oC. PPSU’s superior resistance to hydrolysis also provides longer life over a greater number of cycles regardless of which autoclave temperature is involved.
Both polymers are compatible with ethylene oxide, gamma and plasma sterilization methods, although PPSU provides devices more longevity with its resistance to a greater number of cycles. Another advantage of PPSU is that it withstands hydrogen peroxide sterilization, a shortcoming of PSU. -
Radel PPSU is a proven material for color-coded joint replacement trials because of its exceptional resistance to repeated sterilization cycles. High temperature resistance – Polysulfone and Radel PPSU both resist the practical upper limits of temperatures associated with most medical devices. PPSU however offers greater thermal resistance, a factor behind its superior performance in higher temperature sterilization methods. A good indicator of thermal performance is each material’s glass transition temperature (Tg) or softening point. PSU’s measures 365oF or 185oC, while that of PPSU is considerably higher at 428oF or 220o
- Biocompatibility – This is an area where PSU and PPSU are identical. The standard grades of both can be used for medical devices that are in contact with bodily fluids and tissue short-term, or up to 24 hours. Highly specialized grades of each polymer have also been developed for devices that can be implanted permanently.
- Material composition and cost – PSU and PPSU are high-performance thermoplastics within the same polymer family. PSU consists of linear aromatic chains while PPSU is formed from phenyl rings. This improves PPSU’s hydrolysis resistance, but makes synthesis and conversion slightly more complex, adding to its cost of production. In general terms, however, both materials are priced to the performance value they deliver relative to other medical grade plastics.
Typical Medical Device Applications for Polysulfone (PSU)
Genesis offers polysulfone in Syensqo’s implantable (Eviva) and non-implantable (Udel) medical grades. Both are available in opaque health care colors and light tints that have superior transparency compared to other high-performance medical plastics including PPSU and PEI. In its various forms, medical grade PSU used in several medical instruments and device components, including:
- Dialysis equipment components, such as tubing connectors and filtration cartridges
- Blood oxygenators
- Filtration membranes
- Surgical instruments, including various clamps, forceps and retractors
- Sterilization trays and cassettes
- Medical equipment housings for dialysis machines and monitoring equipment
Its availability in opaque medical industry colors has led to its use as material for color-coded medical instruments that are easy to identify in surgical kits.
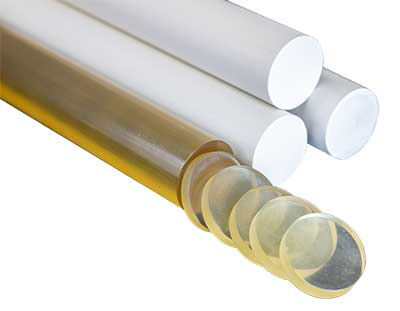
Implantable Eviva PSU is also available in transparent grades, and opaque white. The transparent polymer leaves no imaging artifacts and is therefore a candidate material for devices when imaging is expected following device implantation, such as with orthopedic and neurosurgical implants.
Its long-term biocompatibility also makes implantable grade PSU a candidate for various cardiovascular, neurovascular, dental and drug delivery applications. For example, it is an option as a material for access ports integrated into implantable devices.
Typical Polyphenylsulfone (PPSU) Medical Device Applications
PPSU is the preferred polymer when higher thermal resistance and tolerance to a greater number of sterilization cycles are criteria for a device. Some common applications for the general medical grade PPSU include:
- Medical equipment housings
- A variety of surgical instruments, including forceps, clamps, and endoscopic device handles
- Sterilization containers
- Dialysis components and filters
- Dental devices and components, including orthodontic brackets and dental implant parts
- Medical connectors and fittings
- Valves and shunts
Like PSU, PPSU is available from Syensqo in both a medical grade under the Radel brand for short-term contact with bodily fluids and tissue, and a specialized version designated Zeniva PPSU for long term and permanent implantable devices. Both are available from Genesis in the forms of machinable shapes and as injection molded and machined parts. Zeniva PPSU’s electrical insulation properties also make it a candidate for wire and lead coatings in powered implantable devices.
An Experienced Thermoplastic Converter Can Optimize PSU and PPSU Components for Medical Devices
PSU and PPSU are high-performance medical plastics positioned between advanced polymers like PEEK, and engineering plastics such as polycarbonate and acetal that rank at the lower end of the spectrum of physical properties . They offer a good overall balance of attributes including resistance to most chemicals associated with health care facilities, toughness and durability in finished devices, and compatibility with most forms of sterilization. Their biocompatibility positions them for use in both short-term contact applications as well as long-term and permanently implanted devices.
MDMs that are assessing viable materials for their products may find PSU or PPSU attractive options based on cost and performance. An experienced medical polymer converter can process these specialized plastics under controlled conditions that achieve consistently optimum properties and quality in the finished devices. Those with expertise in this materials processing arena can also be an asset in supporting the MDM on the path to device approval.