Ultem PEI is chemically defined as a polyetherimide. As a medical plastic material, it is available in grades that offer a diverse combination of properties for different medical device applications.
Intrinsically, the Ultem polymer is characterized by high strength, toughness, tolerance to frequent sterilization and resistance to chemicals and cleaning agents used in healthcare facilities. This performance capability has led to its use in many healthcare applications, including:
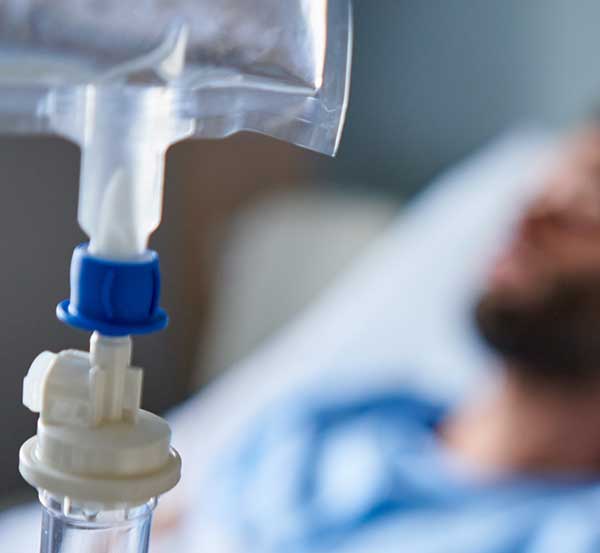
- Rigid medical tubing
- Catheters used in cardiovascular and diagnostic procedures
- Components for angioplasty balloon devices
- Infusion pumps, drug delivery system components
- Structural components and housings for healthcare equipment
- Respirator components
- Radiology systems – particularly radiation therapy equipment
Why Ultem is a Frequent Material Choice for Healthcare Applications?
Various grades in the family of Ultem medical plastics offer a beneficial range of material properties for medical devices and other healthcare applications, including:
- Excellent sterilizability – Ultem PEI is compatible with most sterilization methods and environments, including high-temperature autoclaving, hydrogen peroxide, gamma radiation and UV. Instruments and devices made from Ultem retain dimensional stability and strength following hundreds of sterilization cycles.
- Thermal stability – Ultem PEI has a glass transition temperature (Tg) or softening point of 217oC (422oF). It resists degradation when exposed to high temperature extremes even for extended periods. It also maintains its structural strength at high temperatures even under high physical loads. While few healthcare applications demand this level of thermal stability, the margin of safety ensures that components made from Ultem PEI medical plastics perform reliably under extreme conditions.
- Mechanical strength and impact resistance – Ultem PEI is characterized by excellent tensile and compressive strength and high flexural modulus or rigidity, all of which benefit many healthcare applications. Ultem also offers good inherent impact strength. A recently commercialized grade designated Ultem HU1004 was developed specifically for a step up in toughness for healthcare applications that are exposed to more rigorous handling.
- Biocompatibility – Ultem PEI’s history in medical device applications dates back to the 1980s, serving applications that must meet USP class VI standards. Recently the resin manufacturer introduced two Ultem formulations specifically designated as medical plastics for the healthcare industry. Ultem HU 1000 serves applications that must satisfy ISO 10993 standards for short-term exposure to bodily fluids and tissue, or up to 24 hours. Ultem HU 1004 meets ISO 10993 standards for devices with up to 29 days’ exposure.
- Chemical resistance – The Ultem PEI polymer’s inherently broad resistance to acids, alcohols and aliphatic hydrocarbons is an essential layer of protection for the material’s performance in clinical and laboratory environments. However, it should be noted that variables such as chemical concentration, temperatures and stresses applied to a component can affect performance. Consequently, it is essential to test healthcare components made from any thermoplastic material in the actual environment and under the operating conditions expected to verify efficacy.
-
Ultem PEI medical plastics are injection molded into parts or melt extruded into shapes for machining into prototypes or low production quantities. Production versatility –Ultem PEI is melt-processable by injection molding and extrusion. Injection molding is ideal for manufacturing high quantities that justify the tooling investment. The process consistently and economically reproduces complex configurations, and polished mold surfaces enhance the clarity of transparent components. Melt extrusion yields semi-finished shapes that are machined into precision prototypes or relatively low production quantities. Injection molded parts can also be finish-machined to achieve particularly complex features. Dedicated medical plastics processors with both production methods in-house provide this versatility.
Ultem HU1004 Developed Specifically for Medical Devices
Ultem, like many high-performance medial plastics, is available in a variety of grades for an array of applications. Recently added to the Ultem product family, Ultem HU1004 is a versatile material solution for healthcare applications requiring a greater degree of biocompatibility and improved resistance to hydrolysis compared to other grades.
Specifically, Ultem HU1004 complies with ISO 10993 for devices that are exposed to bodily tissue and fluids for mid-range periods, or up to 29 days. Among its other performance enhancements are its ability to withstand repeated sterilization without notable deterioration. Its color stability after multiple sterilization cycles is also superior to that of some other medical plastics.
Because process conditions affect material performance, specialized medical plastics injection molders and shapes extruders are generally the best resource for ensuring device components achieve the full benefits of high performance medical plastics such as Ultem HU1004.
How Does Ultem PEI Compare to PEEK?
Ultem is frequently compared to other high performance medical plastics during the material selection process. PEEK, also used in many medical devices and other healthcare applications, is often among the material candidates.
PEEK ranks in the top tier of performance among medical polymers. Compared to Ultem, PEEK has better wear characteristics. This can be an advantage in applications that must withstand repeated dynamic loads, such as pivoting. It also resists a wider variety of chemicals.
Ultem offers thermal performance advantages, as its glass transition temperature is 70oC higher than that of PEEK. This translates to better structural stability when required for applications under physical load or stress at higher temperature extremes. Ultem also offers a material cost advantage. PEEK’s impressive material profile comes at a premium, but like all high-performance materials including Ultem, specifiers recognize the value of these materials based on the benefits they deliver for specific application requirements.
An area where PEEK stands apart from Ultem is in implantable plastics. Specialized grades for long-term implantable devices have been developed and are available in the form of extruded shapes for machining precision parts, and as resin for injection molding. Applications include spinal fusion cages, arthroscopy screws and anchors, and tethers for cardiovascular implants. Plastic processors who specialize in extruding shapes and injection molding or machining parts in implantable PEEK on a custom basis for MDM clients provide a valuable service as an option to in-house production by the device manufacturers.
How Does Ultem Compare to Polyphenylsulfone (PPSU)?
PPSU and Ultem are competing materials in the healthcare industry and are often both considered as viable options when developing a medical device because of their performance similarities.
Both materials possess excellent resistance to hydrolysis at high temperatures, which makes them well-suited for applications involving repeated sterilization of implantable applications. PPSU provides superior impact strength and chemical resistance, while Ultem excels in mechanical strength and stiffness. Both have thermal properties that are more than adequate for even high temperature sterilization. Cost-wise, they are similar, depending on the grade specified.
It should also be noted that unlike Ultem PEI, PPSU is available in a specialized grade for non-load bearing, implantable medical devices. Designated Veriva® PPSU, extruded machinable shapes and injection molding resins are available for devices that must meet ISO 10993 for long-term or permanently implanted, devices.
An Experienced Medical Polymer Converter Can Help Achieve Full Value from High Performance Medical Plastics
Ultem PEI can be a cost-effective, performance-reliable and biocompatible medical plastic appropriate for a wide range of healthcare applications. Its combination of toughness, rigidity, hydrolysis and chemical resistance and its compatibility with standard sterilization methods make it a viable candidate especially for devices that must withstand repeated autoclave cycles.
The choice of a medical plastic processor is also an important step in a medical device project involving advanced medical plastics such as Ultem. A specialist in medical plastics can help ensure the full performance benefits of premium materials like Ultem are achieved in injection molded parts and components machined from extruded shapes. Specialized processors also can have close working relationships with medical plastic resin producers and can tap into their extensive application and regulatory data banks to help with application projects and material selection.