Ultem PEI (polyetherimide) is a high-performance thermoplastic introduced in the 1980s. The material offers exceptionally high strength in an amorphous polymer, along with dimensional stability, toughness, high temperature resistance and processability. These attributes, plus its UL 94 VO status and its smoke generation and flammability ratings for use in aircraft components, make Ultem PEI a frequent choice for aerospace, electrical, automotive and industrial applications.
Because of its inherent biocompatibility and sterilization resistance, Ultem PEI has also been specified for a number of medical device applications including surgical instruments, instrument handles and autoclavable trays and carriers. Two grades specifically developed for medical devices, Ultem HU1000 and Ultem HU1004, were added to the Ultem product line, and extend the polymer’s application potential and design opportunities for MDMs. The HU1004 grade is a polymer blend, and as such has somewhat different properties compared to Ultem HU1000, which parallels the physical properties of standard Ultem 1000 PEI.
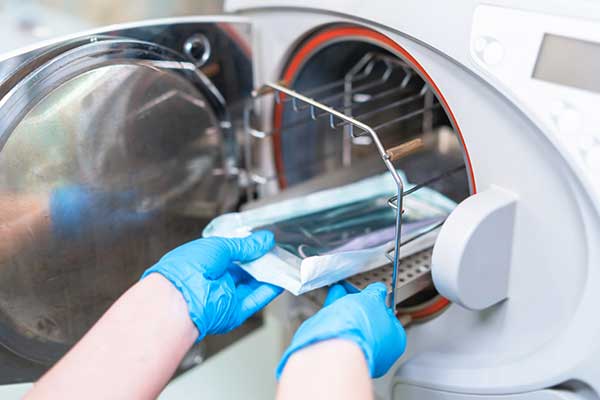
Ultem PEI’s Physical Properties
Ultem PEI is an amorphous thermoplastic in the polyetherimide family of polymers. It’s often compared with PEEK, which is a semi-crystalline polymer. These high-performance materials demonstrate their own unique performance characteristics, and while they are specified for similar applications, each brings benefits related to the individual physical and environmental requirements of each application.
A Brief Comparison of PEEK and Ultem PEI
While Ultem PEI is compatible with a long list of fluids, cleaners and solvents used in hospital and clinical environments, PEEK as a semi-crystalline material can withstand exposure to a greater array of chemicals. PEEK also has the edge on bearing and wear properties. Both materials withstand repeated sterilization by most common methods, and they offer similar levels of rigidity as measured by flexural modulus testing. PEEK offers more impact resistance and toughness according to ASTM notched Izod impact testing. Ultem PEI has the advantage on thermal properties with a glass-transition temperature (Tg) or softening point of 217o C, nearly 70o C greater than that of PEEK. One of the more notable differences is material cost, where the property advantages of PEEK, especially in terms of its chemical and wear resistance, command a premium over Ultem PEI.
Ultem PEI Medical Grades: Performance Profile
Ultem PEI’s unique combination of properties has positioned the thermoplastic as an excellent candidate for sterilizable medical devices. The polymer’s inherent attributes are reflected in the medical grades, Ultem HU1000 and Ultem HU1004. Attributes of the two grades and their differences are noted below.
- Thermal stability – Like many high-performance polymers, Ultem PEI is stable at elevated temperatures well beyond the capabilities of many other medical grade plastics. Its glass transition temperature or softening point of 217o C makes the polymer a good fit for applications such as laboratory and research equipment where prolonged exposure to intense heat under physical load may be required.
Compared to many other medical grade plastics, the HDT or heat deflection temperature under load of both Ultem HU1000 and Ultem HU1004 are also impressive, and relatively similar at 192o C and 196o C respectively.
- Dimensional stability and resistance to hydrolysis- Ultem PEI exhibits excellent dimensional stability over wide temperature variances. Further, all grades have inherently low water absorption and finished parts retain their dimensions very well when exposed to steam repeatedly or for prolonged periods.
- Mechanical strength – The Ultem PEI polymer offers inherently impressive mechanical properties. Its tensile strength, compressive strength and flexural modulus rank high among amorphous thermoplastics. Ultem HU1000 offers approximately 10% higher tensile strength and flexural modulus compared to Ultem HU1004, but both grades can easily satisfy the mechanical requirements of most typical sterilizable medical devices.
- Impact resistance – The PEI polymer has inherently good impact resistance, and provides the durability needed for reusable medical instruments and devices. The proprietary polymer blend formulation of the Ultem HU1004 grade gives it over 35% more impact strength than the Ultem HU1000 and is an excellent option for applications requiring higher durability.
- Biocompatibility – Ultem PEI is ISO 10993 certified, FDA approved for medical use and has been cleared through USP Class VI testing. The medical grades, HU1000 and HU1004, offer two levels of performance in this area. HU1000 can be used for applications in contact with bodily fluids and tissue for up to 24 hours, while the Ultem HU1004 grade extends the exposure limit up to 29 days.
- Sterilizability – The PEI polymer’s compatibility with common sterilization methods translates to the Ultem HU1000 and Ultem HU1004 grades and adds another reason for considering the materials for medical devices and components. They can be sterilized by gamma radiation, hydrogen peroxide, UV and steam autoclaving, including high temperature steam. The materials also retain their physical properties after repeated sterilization cycles.
- Chemical resistance – Ultem PEI offers excellent resistance to alcohols, acids and aliphatic hydrocarbons.
Note: As with all materials considered for a device, components made from Ultem PEI should be tested for compatibility with the chemicals at the temperatures, loads and other variables specific to each application.
- Transparent and opaque colors – Ultem PEI, including the HU1000 and HU1004 medical grades, are transparent amber in their natural form. Custom tints and opaque colors are readily available and can be an advantage for specific devices. The opaque colors provide the benefit of visually differentiating instruments in surgical kits, for example.
- Material forms –All PEI grades including Ultem HU1000 and Ultem HU1004 are available in pelletized form for injection molding and extrusion. Extruded rod and plate are also available for the production of machined parts and prototypes.
Ultem PEI can be injection molded into finished device components, or extruded into semi-finished shapes in the form of rods, plates and tubes for machining into prototypes and commercial quantities of complex precision parts.
Ultem PEI’s Medical Device Applications
The versatile physical properties and inherent compatibility of the Ultem PEI polymer with common sterilization methods make the HU1000 and HU1004 medical grades particularly viable candidates for many applications, including:
- Surgical instruments and instrument handles
- Medical equipment housings and structural components
- Instrument trays, carriers, kits
- Catheter and drug delivery components
- Dental tools and tool handles
- Filters for dialysis machines
- Respirator and ventilator components
In summary, Ultem PEI and the medical grades of the polymer are dependable material options for a wide range of applications in the healthcare industry. They are among the few high-performance polymers that can withstand repeated sterilization and provide the strength and durability required for reliable long-term performance.
A Medical Plastic Processor Can Optimize Device Performance and Quality
High performance polymers like Ultem PEI require process conditions that preserve their physical properties and quality. While the polymer is relatively easy to process, specialized equipment and process controls that monitor and adjust melt conditions instantaneously can avoid process variations and polymer degradation and ensure that components are produced with optimum properties and consistency.
Fortunately, the growth in medical device applications for thermoplastics has led to the establishment of dedicated medical polymer processors who work in close collaboration with their MDM customers. These specialists have invested in the talent, technology and equipment required to achieve the consistently high quality and performance that device manufacturers expect from the premium thermoplastics they specify.