Genesis’ advanced process control technology ensures consistently high quality in medical device components we injection mold from the polymers our customers supply or specify.
Injection Molding Advantages vs. Machining
Genesis customers opt for injection molding as a step up from machining as quantity requirements for their medical grade thermoplastic components grow. The cost of injection molding tooling can be significant, but higher unit volumes usually justify the investment with tooling amortized over the design life of the component. Other factors making injection molding a more attractive option than machining for high volume requirements are the basic costs of making a component. Injection molding offers substantial savings in both material and operator hours compared to machining from a stock shape such as a rod or plate. In addition to these benefits, complex features that require multiple steps in machining can be molded in the component in a single operation.
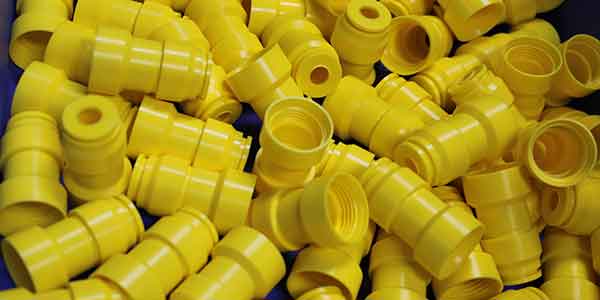
Injection Molding Basics
Prior to molding a medical device component, the thermoplastic polymer is pre-dried in its pelletized form as supplied by our customers. This step removes moisture that can create appearance and performance problems in injection molded components. These polymer pellets are then melted in the barrel of the molding machine. During this phase, temperatures must be carefully controlled to prevent heat degradation of the material. Molten polymer is injected under pressure into the mold cavity where it takes on the dimensions and design intricacies of the component. Lastly, the component solidifies during cooling and is ejected from the mold.
Genesis Injection Molding Capabilities
Genesis’ versatile all-electric injection molding machines have the capacity to produce a wide range of medical device component designs. “Shot” sizes per molding cycle run from 0.03 to 20 oz. (0.85 to 570 grams). These clean-operating machines use no hydraulic systems, eliminating the risk of fluid leakage contamination.
Our process engineers have designed our equipment to be adaptable for molding the wide variety of biocompatible polymers Genesis customers provide. Each machine also has the ability to ‘coin’ or compress components as they are being molded. This unique attribute makes it possible to mold exceptionally heavy sections in components with very low stress and without porosity or voids.
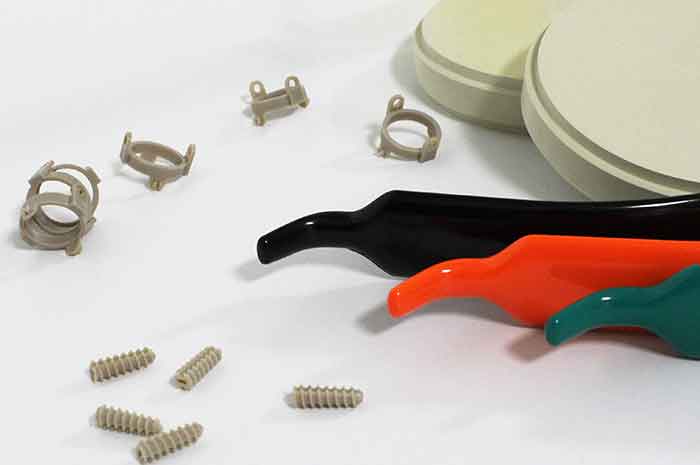
Quality Assurance: ISO 13485 Certification
Genesis Medical Plastics is ISO 13485:2016 certified, an essential element in our ability to service our customers’ requirements. We are an FDA registered device manufacturing facility, which can benefit our injection molding customers. Our production team also utilizes specialized molding equipment and employs extraordinary operating procedures aimed at preventing material contamination throughout the entire molding operation.
All products Genesis manufactures are provided to our customers with Certificates of Conformance at no additional charge.
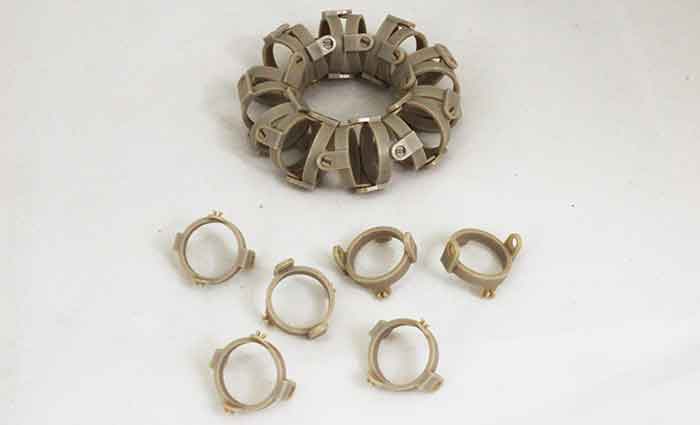
Genesis Technology: Raising the Bar on Quality
Injection molding of consistently high quality medical device components requires effective mold design and tight, reliable process control. The ability to maintain optimum melt temperatures and pressures is essential to achieve the quality and performance expected with biocompatible thermoplastics like implantable PEEK. It is also critical when molding customers’ proprietary polymer formulations that contain specialized performance-modifying additives. These factors are behind Genesis’ investments in the best available equipment and systems technology for injection molding biocompatible thermoplastics. The result is a versatile injection molding capability that can transform our customers’ diverse biocompatible polymers into the consistently high quality medical device components they require.
Our quality-driven shop-floor initiatives and technology investments include:
Optimizing mold design
In DFM (Design for Manufacturing) reviews, Genesis works with customers to define the tolerances, aesthetics and performance required for their medical device components. Our process engineers then can conduct mold flow analysis to validate molding conditions and the best approach to tool design for each polymer formulation.
Clean, versatile all-electric injection molding machines
Once tool design is set, our team defines the best machine configuration and process control conditions for molding each polymer composition. The combination of versatile equipment and materials expertise enables Genesis to transform any class of melt-processable polymer into consistently high quality medical device components.
Many customers tell us our facility is the cleanest and most efficient they’ve experienced. Their feedback is based in part on our production team’s rigid shop floor quality practices. The all-electric injection presses in our facility are another key factor: they use no hydraulics. Our investment in clean electric technology eliminates the risk of hydraulic fluid leakage and potential contamination of materials, finished components and packaging.
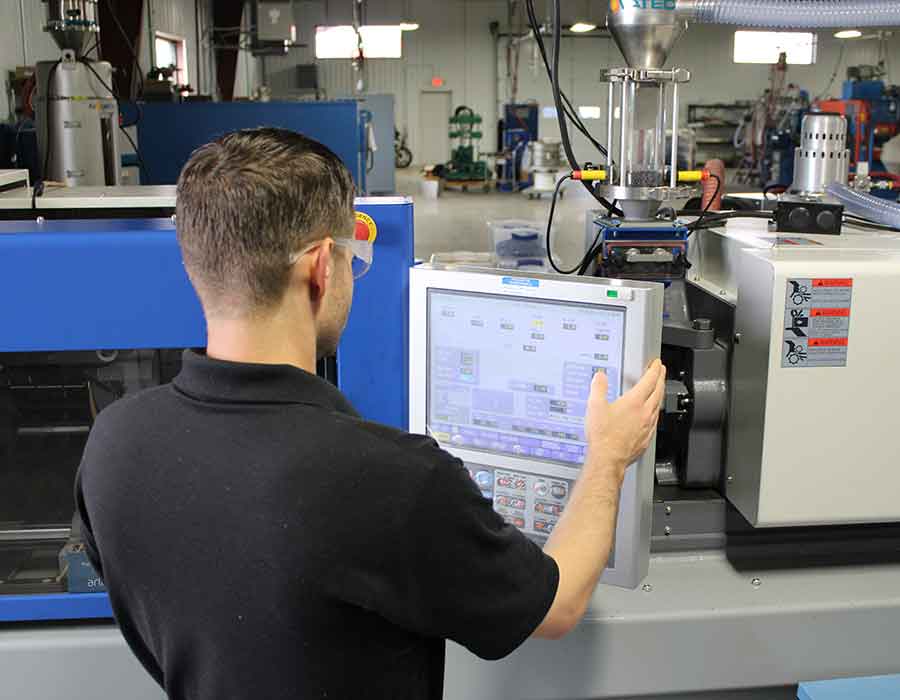
Dedicated dryers
Before the molding process begins, pre-drying medical grade polymers is essential. Each polymer has its own characteristics that dictate its drying conditions. This key step eliminates moisture that will affect component performance and appearance.
During drying, Genesis ensures that pellets remain free from any cross-contamination from other polymers that we process. Polymer pellets are transferred from their shipping containers to Genesis dryers in a closed system to eliminate particulates. These dryers are dedicated to each type of polymer so that thermoplastics with different chemistries do not contaminate the material to be molded. This is particularly important in handling clients’ implantable grades and special medical polymer formulations that require the highest level of integrity in product composition.
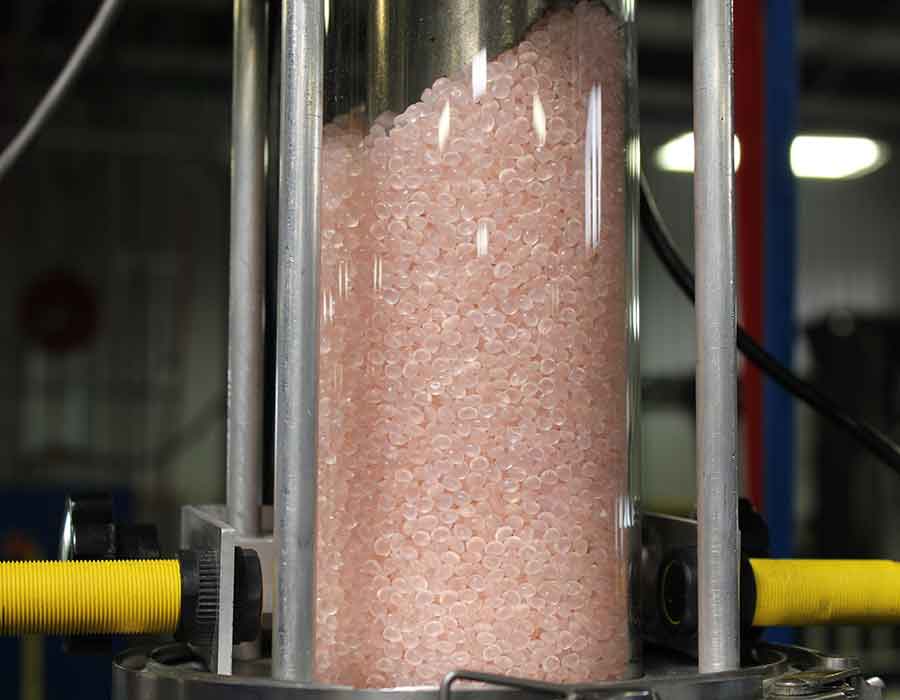
In-mold process control
To ensure the optimum molding conditions specific to each type of polymer, Genesis takes the added step of incorporating pressure transducers and RJG systems within the mold cavity itself. These systems comprise the most comprehensive and effective process monitoring and control technology available for injection molding. They precisely measure process conditions and make instantaneous corrections as needed to maintain ideal pressures and temperatures as components are being molded.
Post-processing quality procedures
When an injection molding production run has been completed, Genesis’ operations team performs a full machine tear-down and clean-up. During this step, all polymer residue is completely removed from every component that was in contact with melted polymer as a final step in eliminating potential sources of contamination in subsequent production runs.
Genesis Mold-Building and Maintenance Services
Genesis offers mold design support that includes the use of mold flow analysis and Design for Manufacturing reviews to optimize customers’ injection molding tooling. Once the design is set, we then utilize our in-house EDM, surface grinding and related capabilities to build the molds. These same capabilities are used to maintain and service molds through their production life. Genesis can also tap into our skilled domestic mold builders if required for highly specialized design features and functionality.
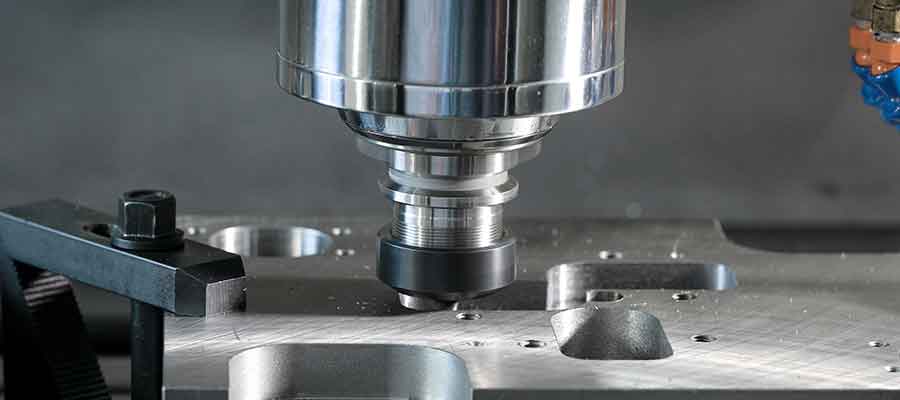
Tooling Cost Factors and Options
Production quantities that make injection molding cost-effective vary with each component’s size, complexity and weight. The vast differences in component configurations make it impractical to offer a general guideline on production quantities that justify the cost of injection molding tooling. However, Genesis routinely works with customers to determine whether injection molding is the best process based on each application.
The total cost of a finished component in the quantities required usually determines whether injection molding or machining is the best option. Several factors play into the equation. Material cost typically favors injection molding, as machining a stock shape into a finished piece involves greater material loss. The ability to amortize the cost of a mold over the intended quantity is a key factor.
Another consideration is design complexity. In some cases, injection molded components require post-machining to achieve features that cannot be molded into the part. When that occurs, economics can favor fully-machining the component unless a design modification can be made to accommodate the capabilities of molding.
Multi-cavity tools that produce several components in each molding cycle are an effective option where clients require high unit volumes from each production run. The cost-efficiency and fast turn-around time for high quantities can easily make the higher tooling investment worthwhile.
Near Net Shape Tooling: a Cost-Effective Transition Step
Machining is an ideal precursor to injection molding early in a medical device’s life cycle or in its market testing and validation stages when quantities are relatively low. Even as quantity requirements grow, they can evolve slowly and keep the investment in production molds out of reach.
Near-net shapes provide an economically attractive transition step between low unit volume machining and high-output injection molding. In this approach, low cost injection molds produce approximate-size blanks without the precision dimensions and tolerances of more costly tooling for full production. Because their dimensions are close to the component’s design specifications, near-net shapes can be finish-machined cost-effectively, quickly and with minimal material loss.
With expertise in both machining and injection molding, Genesis engineers actively work with customers on the best production approach for every stage of a component’s life cycle. Our support team also monitors changes in production requirements over time. We’ll flag opportunities for more cost-effective options like near-net shapes and multi-cavity tooling as requirements evolve.
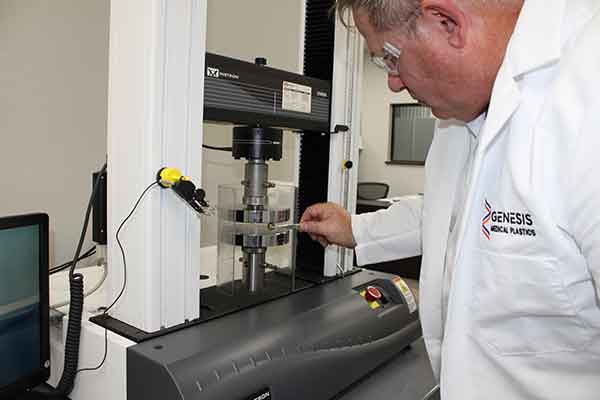
Pre- and Post-production Services and Capabilities
Genesis offers several capabilities services that customers may require for injection molded components:
- ASTM testing to validate mechanical properties.
- Molded ASTM test specimens.
- Laser etching for identification.
- CT (Computerized Tomography) scanning for component inspection.
- CMM (Coordinate Measuring Machine) for dimensional inspection.
- Post-annealing for optimum dimensional stability.
- Ultrasonic cleaning of components.
- Specialty packaging to customer specifications.
- Lot traceability and material certifications.