Home - Why Genesis PEEK - Implantable Genesis PEEK – Comprehensive Overview
Implantable Genesis PEEK – Comprehensive Overview
Genesis PEEK implantable materials include machinable semi-finished shapes, thin sheet and film. All comply with the most current ASTM F2026 requirements for medical devices made from PEEK that are implanted in the human body for 30 days or more. They are extruded from PEEK resin that also complies with ASTM F2026 and in accordance with ISO 10993.
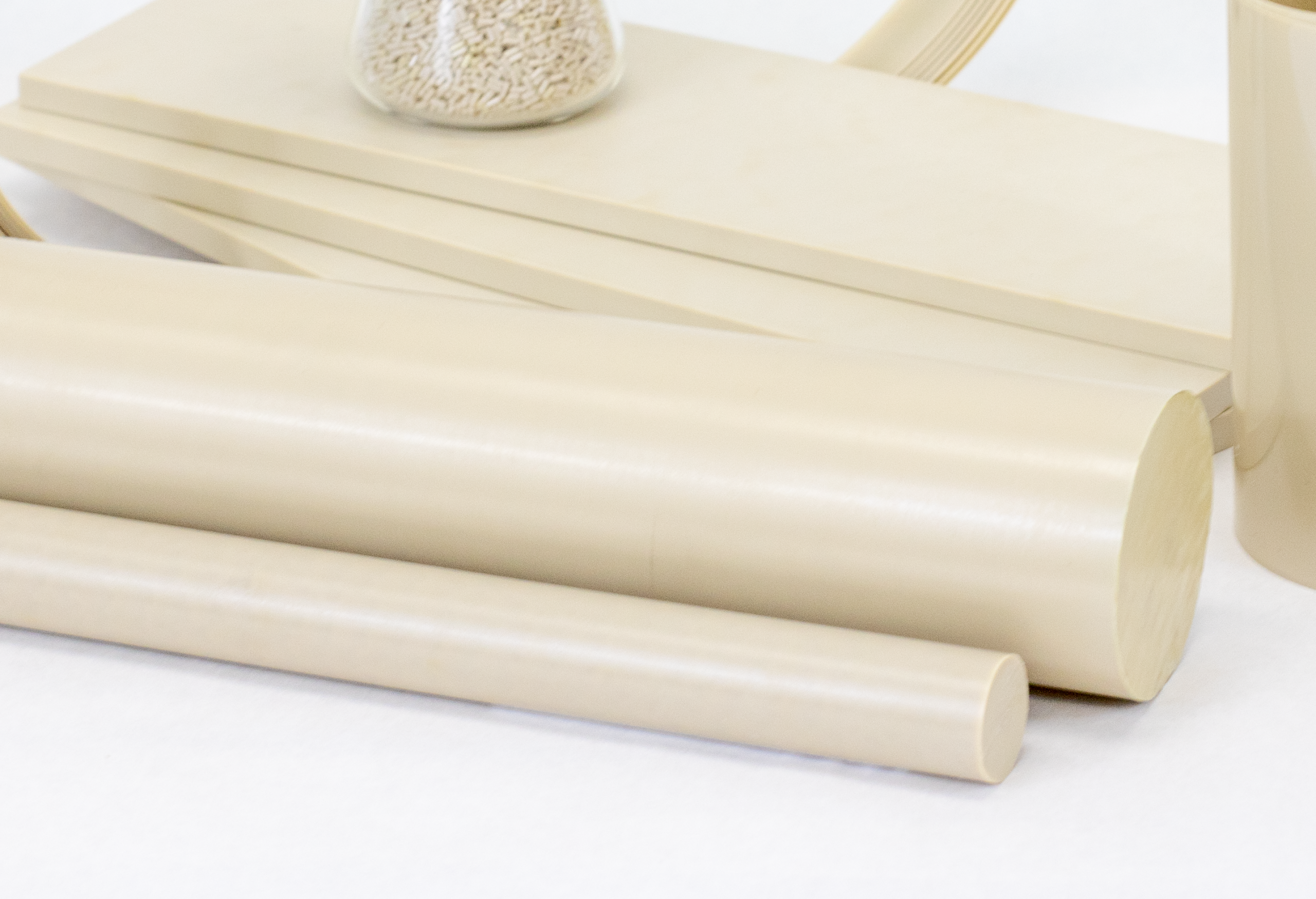
Why Are Genesis PEEK Products a Good Choice for Implantable Devices?
The inherent properties of the PEEK polymer afford a combination of benefits beyond the capabilities of metals and other thermoplastics on several levels. Among its attributes for implantable medical devices:
Physical Strength and Long-Term Stability
Notable advantages of PEEK are its high flexural modulus and resistance to creep under long term physical load. The polymer provides a level of stiffness similar to that of cortical bone which is shown to protect adjacent bone from damage due to stress shielding (Wolff’s Law). Devices made from Genesis implantable semi-finished shapes and film also benefit from PEEK’s inherently high resistance to fatigue failure from repeated flexing. PEEK is also recognized for a level of toughness or ductility that is uncommon in many rigid thermoplastics. This combination makes it an excellent lighter weight option to metals.
Radiolucency
Implanted devices made from Genesis PEEK shapes or film retain the polymer’s inherent radiolucency for accurate CT, MRI and X-ray imaging with generating an imagining artifact which is typically generated when using metals.
Sterilization and Chemical Resistance
PEEK retains its physical properties and biocompatibility after repeated cycles in all common sterilization methods. It is also resistant to chemicals encountered in the medical environment, including isopropyl alcohol and plasticizers used in tubing and other flexible products.
Implantable Genesis PEEK Production Facility and Product Availability
Specifications –
SEMI-FINISHED SHAPES
Rod diameters – mm
- 6; 16; 20; 25; 30; 40
- Custom diameters available
Plate dimensions
- 4mm – 25.4mm
- Maximum width 610mm
FILM
Standard thicknesses – mm
- 125; 0.254; 0.508; 0.762; 1.06
- Custom thicknesses available
Standard width
- 100 mm
- Slit widths, custom lengths available