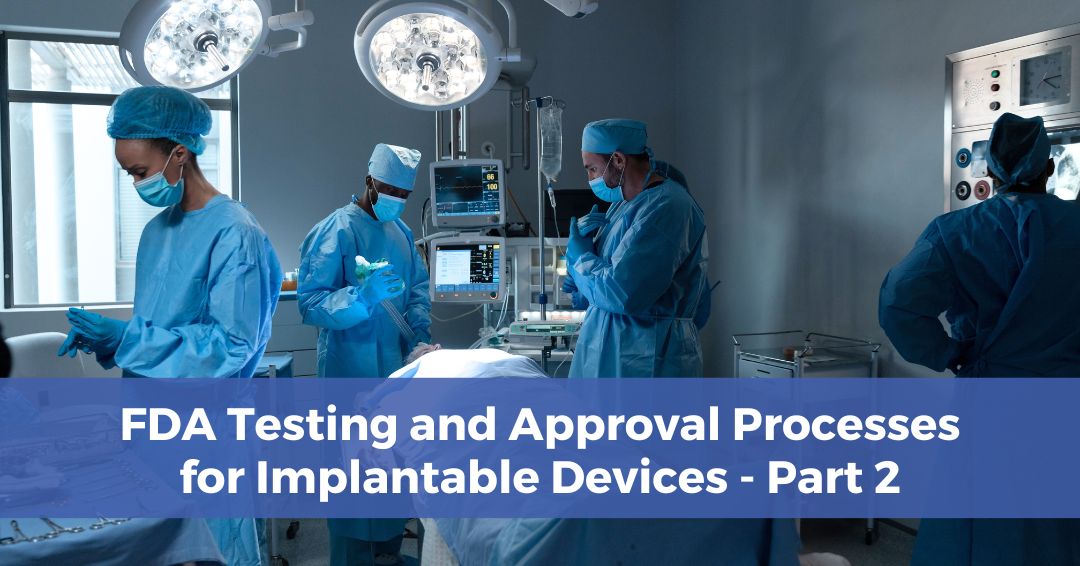
FDA Testing and Approval Processes for Implantable Devices Made from PEEK Polymer – Part 2
Part 2: The 510k Clearance Process Note: This is Part 2 of a Guide to the FDA Regulatory Processes for Implantable Devices Made from PEEK
Part 2: The 510k Clearance Process Note: This is Part 2 of a Guide to the FDA Regulatory Processes for Implantable Devices Made from PEEK
Part 1: The Premarket Approval Process Note: This is Part 1 of a Guide to FDA Approval and Testing Processes for Implantable Devices Made from
What to Consider When Injection Molding PEEK for Medical Devices The injection molding process allows device manufacturers to quickly convert PEEK into complex component designs.
PEEK screws are replacing stainless steel and titanium surgical screws in many instances, and they can be found in various orthopedic and trauma fixation applications.
PEEK and titanium are the primary biomaterials used in fusion cages, but PEEK has a few decisive advantages over titanium. Recently published research also suggests
PEEK’s superior material properties make it a fit for many areas of medicine, including spinal fusion, dentistry, trauma fixation and cardiovascular medicine, among other fields.
For PEEK manufacturers, it’s the physics and materials properties behind the polymer that are most relevant. PEEK’s chemistry is also noteworthy because its chemical structure
PEEK is a thermal isolator, so it does not readily conduct heat into nearby materials. It’s also an ideal electrical isolator, and together, these properties