Many medical devices are manufactured using injection molding, or by CNC machining semi-finished extruded shapes. There’s a place for each production method, and ideally a medical plastics processor will be experienced and capable in all the technologies.
Injection molding offers several advantages for medical devices, including:
- Cost efficiency at higher production volumes
- Faster output of higher production volumes than machining
- Ability to reproduce complex device geometries
- Excellent repeatability and tight tolerances
- Reduced waste
Perhaps most importantly, the injection molding manufacturing process is compatible with an impressive range of polymers, including high performance medical grade plastics. This includes implantable medical polymers based on PEEK, PSU and PPSU.
When quantities for performance validation, market testing or regulatory submittals reach high enough levels, injection molding can also be used to produce prototypes or pre-production parts in larger quantities. Fine-tuning of the injection molding tooling can then be accomplished as market feedback or test results dictate, as a prelude to full production.
The following provides a closer look at the many advantages of injection molding, and how the production process and specialists in the technology can best serve the needs of MDMs.
Injection Molding is Cost-Efficient for High-Volume Medical Device Production
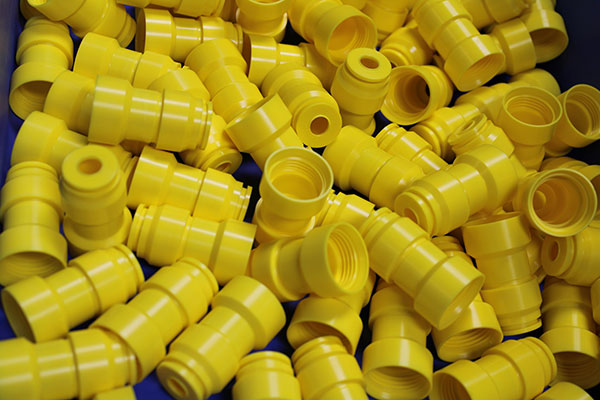
Injection molding is cost effective compared to machining on a per-part basis because it delivers production-scale quantities much more quickly and with less material utilization. The process requires an initial investment in tooling which is usually substantial, but the potential for amortization is often done even in the planning stages based on demand forecasts.
In some cases, MDMs will move from machining to injection molding when unit volumes justify the cost of the tooling. In other instances, while volumes are still low, MDMs may know that production demand will justify the tooling investment at a predictable point and proceed directly from machined prototypes to injection molded devices.
Injection molding is also often used by manufacturers in a pilot phase, where large volumes of prototypes may be entered into market test programs at medical facilities. Typically, molds can be modified to final specifications and dimensions based on feedback from those evaluations.
Injection Molding Can Quickly Adjust from Prototyping to Full Production
High production volumes may often be needed during late-stage prototyping to acquire feedback data in such critical areas as patient safety and functional usability.
From that juncture in product development, the ability to scale up to full production quantities relatively quickly becomes another advantage of injection molding. Even if small design changes are warranted based on market feedback, tools can be modified quickly by a capable specialist in injection molding medical plastics. This allows an efficient transition from prototyping and market testing to full commercialization.
Injection Molding Consistently Reproduces Complex Geometries Designed in Medical Grade Plastics
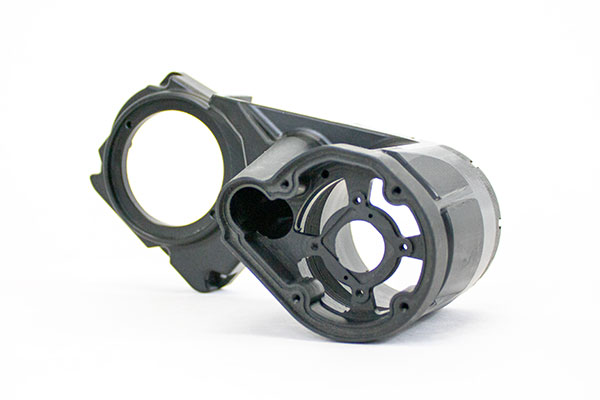
Although machining can achieve closer tolerances and replicate designs that are more difficult to mold, injection molding is also effective at producing highly complex configurations, and can do so with a high degree of design repeatability and consistent quality. Features such as thin wall sections, corners with tight radii, helical or spiral features and complex surface textures can be molded in a single-step process.
Achieving highly complex designs and maintaining consistency in performance and dimensional tolerances requires a working knowledge of the melt flow behavior of the medical plastic specified. A molder with state-of-the-art melt-flow analytical equipment can determine the melt-process conditions that will preserve a plastic’s properties, and how the material will flow within a specific injection molding tool. An investment in process controls to maintain constant conditions with real-time feedback on melt pressures and temperatures is also essential to assuring consistent quality and performance throughout each run, and from run to run.
Post-machining Molded Parts Can Provide More Complexity When Needed
In some cases, medical devices are designed with certain features that injection molding alone cannot achieve. A medical plastics production specialist with comprehensive production facilities for injection molding and CNC machining can resolve these situations. In most cases, the post-machining operation can be done quickly and with minimal material loss given that the desired part configuration is almost fully achieved by molding and requires only minor machining work.
Injection Molding is a Low Material Utilization
Injection molded parts typically are produced to the desired configuration with no post operation other than trimming off the sprues or runners. Additionally, with proper process conditions and clean materials handling equipment and procedures, these trimmed pieces may often be ground and blended in small quantities with virgin pellets without affecting quality or performance of the molded device.
Injection Molding Technology Opens the Full Spectrum of Medical Plastics to MDMs
State-of-the-art injection molding and process control equipment coupled with expertise in medical plastics melt behavior open a wide range of plastics to MDMs, with many positive outcomes. For example, strong, tough polymers that withstand repeated sterilization have enabled complex innovative instrument and device designs that are more economical and faster to manufacture than many metals, and have the added benefit of lighter weight and radiolucency. Implantable grades of high-performance, medical grade plastics are also now used in injection molded devices approved for contact with bodily fluids and tissue long-term, defined as 30 days or more.
In addition to the more advanced plastics, several strong, tough materials serve a diverse array of single- and multi-use applications, all produced economically and with consistent quality by injection molding. Among the medical grade plastics specified for injection molded single-use components as well as devices that go through hundreds of sterilization cycles:
- Polyarylamide (PARA)
- Polycarbonate (PC)
- Polypropylene (PP)
- Polyvinyl chloride (PVC)
- Polysulfone (PSU)
- Polyphenylsulfone (PPSU)
Combining the Benefits of Medical Plastics and Injection Molding Expertise
MDMs have access to a diverse array of injection moldable medical grade plastics that can open the door to more innovative, functional and economical devices.
Once the polymer is specified, partnering with an experienced and well-equipped medical plastics injection molder can yield beneficial returns. A capable processor will help determine the best approach to designing, building and maintaining tooling. In addition, an injection molder with a versatile array of equipment can right-size the molding machine to the part configuration and quantities required, enabling MDMs to meet lead-time and cost targets consistently. A company recognized for best-in-class medical plastics injection molding technology will also have strong working relationships with the leading medical plastics resin producers, and provide MDM customers with support on materials information and a window into new polymer developments that may open paths to future medical device innovations.