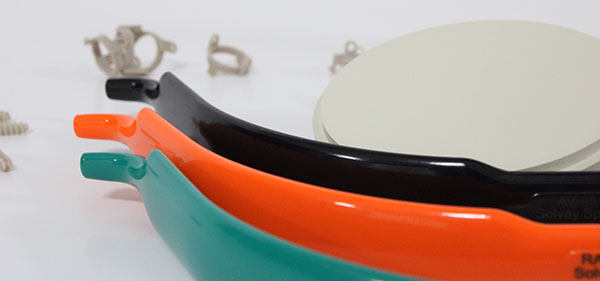
Polysulfone (PSU) is a medical grade plastic that offers an impressive combination of biocompatibility, durability and compatibility with most sterilization options. Its overall balance of performance and economics has made it a prime candidate among the plastics used in healthcare devices that must withstand hundreds of sterilization cycles.
When evaluating materials, medical device manufacturers (MDMs) have an array of options in medical plastics. They include polymers that can be used for devices requiring regulatory approval for limited or short-term (up to 24 hours) contact with to bodily tissue and fluids, and for devices that are implanted longer term or permanently. Polysulfone is one of the few polymers that is available in grades for both levels of biocompatibility.
Medical grade plastics for short-term exposure devices
The major medical grade plastics and brands for devices requiring approval for short-term exposure include:
Polymer family
|
Tradename
|
Polysulfone (PSU)
|
|
Polyphenylsulfone (PPSU)
|
|
KetaSpire; Victrex; VESTAKEEP Care
|
|
Polyetherimide (PEI)
|
|
Polyarylamide (PARA)
|
|
Polycarbonate (PC)
|
Makrolon
|
Polyoxymethylene (POM)
|
<Several>
|
Medical grade plastics for long-term and permanent implantation devices
Specialized polymer resin grades that can be used in longer-term and permanently implanted devices is a more limited group. It includes Syensqo Solviva Biomaterials’ Zeniva PEEK, Eviva PSU and Veriva® PPSU; Invibio Biomaterial Solutions’ PEEK Optima, Evonik’s VESTAKEEP Implant PEEK, and Superior Polymers’ Magnolia PEEK. Genesis Medical Plastics also offers implantable PEEK machinable stock shapes, film and thin sheet under the Genesis PEEK brand.
Each of these medical plastics has properties and attributes that make it well-suited to the performance requirements of specific healthcare devices. They also may relate to how the MDM plans to position a device in the market relative to prior versions, or in comparison to competitors’ products.
In addition to biocompatibility, performance-related factors behind the material specification for a device may include rigidity, toughness or durability, chemical and temperature resistance, and longevity over a targeted number of sterilization cycles in various methods. Other factors in material selection might relate to aesthetics, an area where plastics offer several advantages over metals. For example, transparency may be important for drug delivery devices, while custom opaque colors might be a marketable advantage for differentiating instruments in surgical procedure kits.
Polysulfone’s Key Properties and Performance
Polysulfone is recognized by medical device manufacturers for its robust balance of properties that make it a good candidate for a variety of healthcare applications. Its characteristics include:
- Biocompatibility – Polysulfone has a long and proven history in medical devices that are biocompatible for short-term or up to 24-hour tissue contact. A grade of the polymer has also been developed for implantable medical devices requiring approval for long-term exposure to internal bodily tissue and fluids. Commercialized as Eviva PSU, the implantable grade is manufactured by Syensqo under stringent quality and production procedures in ISO 13485 facilities and passed an extensive battery of regulatory tests for long term biocompatibility. The resin manufacturer supports MDMs with FDA file access related to these tests.
- Multi-cycle sterilization resistance – Polysulfone has broad-spectrum sterilization compatibility with its combination of thermal, chemical and hydrolysis resistance. It withstands autoclaving at 250oF/121oC for hundreds of cycles and can be sterilized multiple times at in autoclave systems with higher temperature steam at 273oF/134o. Devices made from polysulfone also retain their properties after multiple cycles in ethylene oxide gas and gamma systems.
- Durability and chemical resistance in the healthcare environment – Polysulfone provides the combination of toughness and stiffness that make it a good choice for instruments and trays that must be sturdy and survive rough handling – or when dropped. The polymer also resists many cleaners and chemicals commonly used in healthcare facilities.
Note: Different concentration levels and temperatures can affect a plastic’s resistance to a specific chemical. The degree of applied load or stress on the device can also be a factor. Best practice with any material is to validate performance by testing prototypes or production parts in the actual application environment.
How Polysulfone Compares to Other Short-term Biocompatible Plastics
Polysulfone compares favorably to most healthcare polymers specified for devices that are in short-term (up to 24 hour) contact with bodily tissue and fluids. Each of these polymers has a unique profile of physical properties and attributes that satisfy specific performance requirements of a wide variety of devices. Other medical plastics in this category include:
-
While both are sulfone polymers, PSU’s lighter tint (left) is often preferred over PPSU (right) where transparency is important. Polyphenylsulfone (PPSU) – PPSU is commonly referred to by its Radel brand and has been available for decades in grades that serve short-term biocompatible devices. One of its advantages over PSU is its ability to withstand far more cycles in high temperature autoclaving at 273oF/134o. Both materials are used for instruments and instrument handles and similar applications based on the desired sterilization life of the device. PPSU is also the leading material for sterilizable joint replacement trials. It is more ductile than PSU, but less rigid. The polymer has a natural darker amber tint compared to the very light yellow tint of PSU. Both are available in opaque healthcare colors.
-
Polyetherimide (PEI) – Also recognized by its Ultem tradename, PEI is used in applications where mechanical strength at high temperatures and chemical resistance are important. It is more rigid than polysulfone, but it has lower impact resistance, an important consideration where frequent handling may require higher durability. PEI is transparent dark amber in its natural form and is available in opaque colors. Typical applications include sterilization and radiation therapy equipment, as well as infusion pumps and components for respiratory devices.
-
Polyarylamide (PARA) – Ixef PARA serves single-use healthcare instruments with its high strength and stiffness and a glossy surface when injection molded. It is reinforced with glass fibers to maximize its rigidity and is available in a wide spectrum of opaque colors. Unlike polysulfone, PARA does not withstand repeated autoclaving. Because parts can be injection molded in large quantities with consistent quality and precision tolerances, it is a cost-efficient alternative to machined metals for single-use devices.
- Polyoxymethylene (POM-C) – Polyoxymethylene copolymer is also referred to as acetal or POM-C. It is used selectively in healthcare applications due to its lack of resistance to multiple sterilization cycles, an area where polysulfone excels. However, medical devices sanitized with disinfectants or sterilized in a limited number of low temperature steam or gamma cycles are good candidates for POM-C. The opaque polymer is available in a range of colors and is a lower cost material compared to polysulfone. Insulin pens are a typical POM-C application.
- Polycarbonate (PC) – PC is a clear polymer with the highest impact resistance among medical plastics. Its clarity and toughness as a protective material are advantageous for healthcare applications such as break-resistant incubator covers. Medical polycarbonate grades are specified for clear applications requiring short-term biocompatibility, such as injection-molded blood oxygenators, fluid transfer and drug delivery devices, and lower production quantity machined devices such as valve bodies. It can be sterilized a limited number of times in ethylene oxide and gamma irradiation media, but it does not have the hydrolysis resistance of PSU and is not recommended for steam sterilization (autoclave).
How Polysulfone Compares to Other Long-term Implantable Polymers
A specialized grade designated Eviva PSU is among the select group of long-term biocompatible materials. The others are:
- Implantable polyetheretherketone (PEEK) – Implantable PEEK has gained worldwide acceptance based on decades of proven use in long-term and permanently implanted devices. Successful applications include spinal fusion cages, cardiovascular anchor tethers and connectors, dental and orthopedic implants and implantable bio-electronic devices.
Implantable Eviva polysulfone resin and machinable shapes are available in a light transparent tint and opaque white. A major benefit of implantable PEEK compared to traditional metals is its Young’s elastic modulus which is similar to that of human cortical and trabecular bone. This physical property of PEEK helps avoid adjacent bone weaking due to stress shielding while facilitating healing of nearby bone injuries. PEEK’s radiolucency also allows clear imaging in areas in proximity to implanted medical devices made from the polymer.
Developments in PEEK include grades with additives that extend the benefits of the implantable material to other applications. A PEEK formulation with barium sulfate added to augment imaging contrast is a notable example.
Compared to PEEK, implantable PSU offers less rigidity, making it more suitable for devices that are non-structural or non-load bearing. While PEEK is opaque, PSU is available in opaque white and in a very light natural transparent tint. Its transparency gives designers an option for devices where visual clarity is beneficial. - Implantable polyphenylsulfone (PPSU) – Polyphenylsulfone, developed as an implantable polymer under the Veriva® trade name, is similar to polysulfone in chemistry. However, it provides higher temperature resistance and impact strength. In addition to its biocompatibility, Veriva® PPSU’s electrical properties and chemical resistance make it a candidate material for insulators, including wire and lead coatings.
The Wide Range of Applications for Biocompatible Grades of Polysulfone
Polysulfone’s performance characteristics have led to its use in a wide variety of short-term exposure healthcare applications. The development of an implantable grade in both opaque and transparent forms extends its application potential.
Devices for short-term (≤ 24 hours) contact with bodily fluids and tissues
- Filtration membranes
- Surgical instruments and instrument handles
- Surgical trays and kits
- Medical equipment housings and components
- Blood oxygenators
- Dialysis equipment filters and tubing
- Drug delivery fittings and connectors
- Sterilization trays
Devices requiring biocompatibility for long-term or permanent contact
Syensqo’s Implantable Eviva PSU opens the possibility for new long-term implantable devices where transparency can be beneficial. Potential applications in transparent and opaque forms include:
- Ventriculoperitoneal, ventriculoarterial and lumboperitoneal shunts
- Cardiovascular stents
- Dental implants
A Unique High-Performance Medical Polymer with Broad Biocompatibility
PSU is appropriate for an array of medical devices and components that are in contact with bodily fluids and tissue short-term or are implanted long term. Its very light transparent tint sets it apart from other biocompatible polymers. While it does not have the high structural rigidity of PEEK, it is a viable candidate for non-load bearing components and devices where repeated sterilization, clarity and ductility are important criteria.
Medical device manufacturers can derive considerable value by working with a polymer converter who specializes in PSU and other medical plastics and has the versatile operations to produce them in different forms. A capable resource can help define performance differences between PSU and other polymers related to the requirements of a device. A processor with versatile capabilities and FDA registered as a device manufacturing facility can also provide MDMs with extruded machinable shapes, machined prototypes, and production parts made by machining and by injection molding. These combined capabilities can help designers evaluate candidate materials options, provide quick turn-around on prototypes and parts for testing, and shorten the path to final material specification.