PEEK is a high-performance polymer that offers several advantages to medical device manufacturers and those who benefit from innovative products in the healthcare industry. Those advantages include:
- Biocompatibility that satisfies the most stringent regulations
- Ideal rigidity, with a flexural modulus that simulates cortical bone
- Sterilization compatibility and resistance
- Radiolucency
- Compatibility with performance-modifying additives
PEEK is one of the few medical polymers available in grades for devices with short-term (up to 24 hours) contact with bodily fluids and tissue, and in specialized grades that are appropriate for long term and permanently implanted devices. Already widely accepted worldwide as versatile medical device material, it has the potential to open many more innovations in the medical industry for several reasons. The following addresses each of the medical plastic’s advantages in detail and how they have established PEEK as a frontline option for current and promising new healthcare applications.
PEEK’s Biocompatibility
Before they can be used for healthcare devices and equipment, all medical materials must be assessed for their biocompatibility and approved by the FDA and other regulatory agencies based on rigorous testing. PEEK has been approved through this protocol and backed by decades of patient case studies and lab testing that confirm its viability. This includes studies based on testing in the following categories that validates its biocompatibility:
-
Implantable PEEK is available as pellets for injection molding and other melt processes, as well as in the form of film and stock shapes for machining precision parts. Sensitization and irritation
- Cytotoxicity
- Genotoxicity
- System toxicity: acute, sub-chronic and chronic
- Hemocompatibility
- Carcinogenicity
PEEK’s broad and well-validated biocompatibility supports its growing use as a material for permanent implant applications. Case studies, some involving patients with devices made from PEEK that have been implanted for more than 20 years, confirm the material’s efficacy in these critical applications.
PEEK’s Ideal Flexural Modulus
A material’s modulus refers to its degree of structural rigidity or flexibility, an important characteristic for MDMs to consider depending on the intended function of a device. PEEK’s modulus is ideal for many implanted applications, for example, because its flexural modulus is similar to cortical bone – the part of the bone that performs the load- bearing function.
When PEEK is injection molded or machined into weight-bearing medical devices and components, its cortical bone-like modulus affords a major benefit compared to titanium. The high level of rigidity in implants made from titanium shields the body from weight-bearing stresses to a degree that slows bone regrowth and re-strengthening. PEEK’s flexural modulus however sits in a Goldilocks zone: it has just the right load-bearing properties and modulus that allow enough tissue-stimulating force to promote bone strengthening and healing.
PEEK’s Sterilization Compatibility and Resistance
Many medical devices and instruments are subjected to regular sterilization, a process that can negatively affect plastics after repeated cycles. High-temperature autoclaving, for example, quickly deteriorates the properties of polycarbonate and polyethylene.
PEEK is among the few medical polymers, along with polysulfone and polyphenylene sulfide, that exhibit excellent resistance to all forms of sterilization, including:
- Autoclaving – including systems using high temperature steam
- Gamma radiation and electron beam sterilization
- Ethylene oxide gas
PEEK’s inherent ability to retain its properties after hundreds of autoclave cycles in these methods means instruments and components made from the material can be sterilized confidently in systems common to most medical facilities.
PEEK’s Radiolucency
In unfilled grades, PEEK is fully radiolucent. It does not produce artifacts on X-ray, MRI or CT scans. For applications where the surgical team must monitor patient progress, its radiolucency ensures physicians get a clear picture of the treatment area.
PEEK’s Compatibility with Performance-enhancing Additives
Like many engineering and high-performance plastics, additives can be fully blended into the PEEK polymer to impart specific characteristics that may be desirable in a device. Barium sulfate, for example, can be added to PEEK to increase its radiopacity, an attribute that allows physicians to routinely monitor implanted devices.
Another common additive is carbon fiber, which can be integrated into the PEEK polymer to increase its stiffness. Highly rigid formulations with 20% and 30% carbon fiber content are most often used in load-bearing orthopedic and trauma fixation devices.
PEEK’s Medical Applications
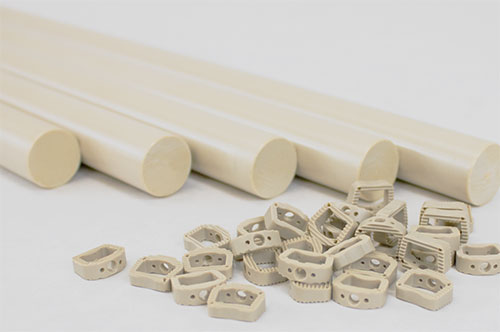
PEEK’s performance benefits make it a strong candidate for many healthcare applications, including:
- Spinal implants, including interbody fusion cages
- Cardiovascular devices, including replacement heart valves
- Orthopedic implants, including hip and knee replacements
- Dental implants, including abutments and dental frames for replacement dentures
- Trauma fixation plates and hardware, typically used for repairing bone fractures
- Endoscopic parts, where radiolucency is particularly important
- Various surgical instruments and drug delivery components
PEEK’s presence in healthcare has expanded greatly in recent decades, and researchers are working to unlock more innovations made possible by the material and its compatibility with additives. For example, some MDMs are developing devices made from PEEK with hydroxyapatite (HA) added as a bioactive agent to improve efficacy in bone regeneration.
An Experienced Polymer Converter Can be a Valuable Resource
PEEK’s material properties provide numerous benefits for devices including broad biocompatibility, a unique and beneficial flexural modulus, sterilization resistance, radiolucency and compatibility with performance-enhancing additives.
The challenge for MDMs is how to capture these advantages consistently and effectively. Converting high performance medical polymers into injection molded or machined components that retain their desired properties requires a combination of process engineering expertise, specialized equipment and rigid process control. The level of investment in the talent, hardware and space necessary is often beyond the reach of MDMs who may have an innovative device design, but not the required production resources. There are also specialized conversion processes that may be required or desirable, such as the extrusion of machinable shapes coupled with CNC machining to develop prototypes.
The investment level required may also divert an MDM from their key priorities in design, development and the work required for regulatory approval. these are among the reasons why MDMs often partner with a dedicated medical plastic converter to develop and provide the manufacturing resources required. Such collaborative relationships allow MDMs to fully focus their talent and capital investments on their strengths and priorities while device production proceeds at reliable supply levels with consistently high quality and performance.